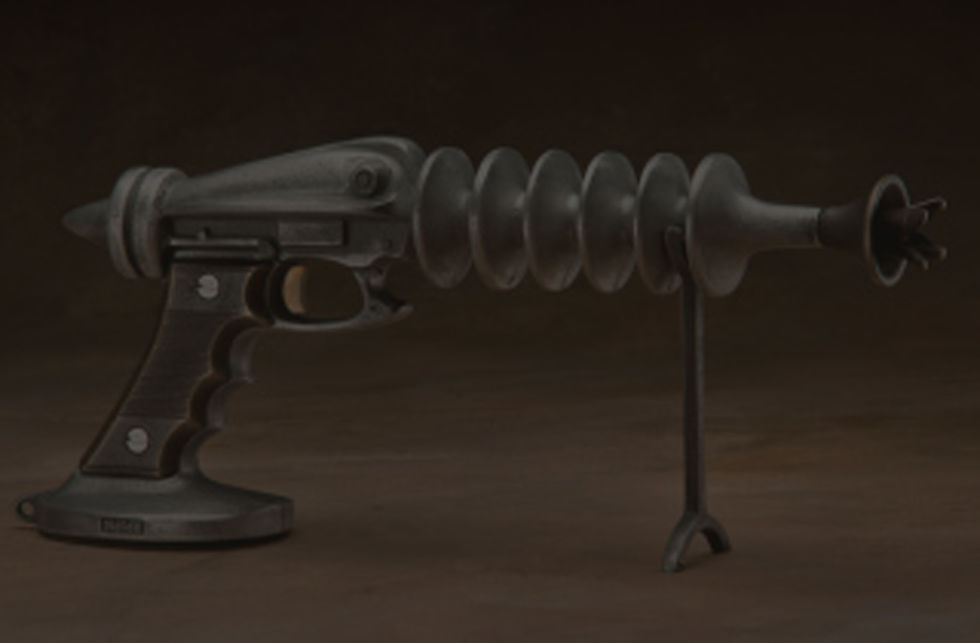
Scott Nelles
Generally I develop my sculptures with some rough paper sketches or create them directly in three dimensions. Though I have utilized different techniques of casting such as the “lost wax method”, I generally work in the “sand casting method.” To be a sculptor and founder of bronze entails many skills and the use of many materials. Some people work only in wood, others work in clay or glass. I work in a variety of materials to develop a pattern or model of my sculpture. I might make a model with wax or oil based clays, some are very soft and some are very hard. Other materials important to the “pattern-making” stage are wood, plastics and resins of all kinds. Sheet metal and fabrication, welding and forging all come into play. When a concept is created in one of my materials or combination of materials, I then need to make a series of molds of the original model. These molds can be made in plaster, various poured resin materials, or sand. Then I have a final pattern made in a rigid material like polyurethane plastic or cast aluminum. Using this pattern called a “match plate,” I can make rammed sand molds off of it in the foundry. Then I cast the bronze at 2150 degrees F into these sand molds. When the metal cools, we shake the sand away and a rough casting of my original sculpture emerges. Many types of finishing operations follow. They include cutting, belt sanding, die grinding, sand blasting, tumbling, oxidizing, polishing and lacquering.
Many people ask me if all my current works are limited editions, they are not in the strictest sense. I cannot afford to limit the number I finally produce because it can take hundreds of hours to make the first prototype. All my work is made by hand in my own studio and that alone assures their limited production. Currently, I have been concentrating on a line of cast toys. I love the art deco period and I believe my toy cars, boats, rockets and airplanes reflect that love. Like most artists, my interests continually change and evolve.

